Wire EDM (Electrical Discharge Machining)
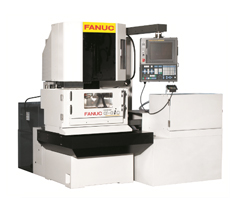
Wire EDM (Electrical Discharge Machining)
Our Wire EDM (Electrical Discharge Machining) capabilities are designed to meet the highest standards of precision and efficiency. With our advanced Wire EDM technology, we can create intricate and complex shapes with exceptional accuracy. Our machines are capable of handling parts up to 16 inches in height, making us well-equipped to tackle a wide range of projects. Whether you need prototypes, small batch production, or high-volume manufacturing, our Wire EDM services deliver consistent and reliable results.
We pride ourselves on achieving tight tolerances, ensuring that every part meets your exact specifications. Our Wire EDM process can achieve tolerances as tight as ±0.005mm, providing the precision required for even the most demanding applications. We utilize a variety of EDM wire diameters, including 0.1mm, 0.15mm, 0.2mm, 0.25mm, and 0.3mm, allowing us to tailor our approach to the specific needs of your project. Trust us to deliver high-quality, precise components that meet your requirements and exceed your expectations.
Wire Electrical Discharge Machining (Wire EDM)
Wire Electrical Discharge Machining (Wire EDM) is a non-traditional machining process that uses electrical discharges (sparks) to cut and shape materials. This process is particularly effective for machining hard, brittle, or delicate materials that are difficult to machine using conventional methods.
How Wire EDM Works
Wire EDM operates by generating a series of rapid, repeating electrical discharges between a thin wire electrode and the workpiece, both of which are submerged in a dielectric fluid. The wire, typically made of brass, copper, or tungsten, is strung between two spools and moves along a programmed path. As the electrical discharges occur, they erode material from the workpiece in a precise pattern, allowing for the creation of intricate shapes and features[1][2].
The dielectric fluid serves multiple purposes: it cools the work area, removes eroded material, and acts as an insulator until the electrical discharge occurs. This process ensures that the wire never actually touches the workpiece, preventing any mechanical stress or deformation[2].
Advantages of Wire EDM
- Precision and Accuracy: Wire EDM is renowned for its ability to produce highly accurate and precise cuts. It can achieve tolerances as tight as 0.005 mm and surface finishes up to 0.8 µm, making it ideal for applications requiring intricate details and high dimensional accuracy[2][3].
- Complex Geometries: Wire EDM can cut complex contours, slots, holes, and 3D profiles that would be challenging or impossible to achieve with conventional machining methods. This capability is particularly valuable in industries such as aerospace, medical device manufacturing, and tool and die making[2][4].
- Material Versatility: Wire EDM can machine a wide range of electrically conductive materials, including hardened steels, carbides, titanium, and superalloys. This versatility makes it suitable for applications involving hard or exotic materials that are difficult to machine using traditional methods[2][3].
- No Mechanical Stress: Since Wire EDM is a non-contact process, it generates no cutting forces or vibrations. This allows for the machining of delicate or thin-walled components without the risk of deformation or damage[2][4].
- Minimal Material Waste: The Wire EDM process produces minimal material waste, as it only removes material along the path of the wire. This efficiency is beneficial for both cost savings and environmental considerations[4].
- Reduced Tooling Costs: Wire EDM does not require custom tooling, which reduces setup and changeover times. New parts can be quickly produced by simply programming the CNC path, making the process highly adaptable and cost-effective for small batch production or prototyping[2][4].
- Surface Integrity: The Wire EDM process produces a high-quality surface finish with minimal thermal damage to the workpiece. This reduces the need for additional finishing operations and helps maintain the integrity of the material[3][4].
Applications of Wire EDM
Wire EDM is widely used in various industries for applications that require precision and complexity. Some common applications include:
- Aerospace: Manufacturing of turbine blades, fuel system components, and other critical parts that require high precision and complex geometries.
- Medical Devices: Production of surgical instruments, implants, and other medical components that demand intricate shapes and tight tolerances.
- Tool and Die Making: Creation of molds, dies, and punches for injection molding, metal stamping, and extrusion processes.
- Electronics: Fabrication of micro-components and intricate parts for electronic devices and circuits.
Wire EDM is a powerful and versatile machining process that offers numerous advantages over traditional methods. Its ability to produce precise, complex shapes with minimal material waste and no mechanical stress makes it an invaluable tool in various high-tech industries. By leveraging the unique capabilities of Wire EDM, manufacturers can achieve superior quality and efficiency in their production processes.
References[1] Electrical discharge machining - Wikipedia[2] Wire EDM Explained: Everything You Need to Know - Unionfab[3] What is Wire EDM Cutting, its advantages & limitations? - Material Welding[4] Benefits of Wire EDM Cut-Process, Advantages & Applications - ProleanTech[5] How Does Wire EDM Work? Definition, Process & Applications | Owens ...[6] Wire EDM. Guide to EDM Wirecut Machine, Process & Uses
With over 20 years in business and over 36 years of experience.
Contact us today about your manufacturing needs.